Commodities Special
PAY OVER THE NEXT 3 YEARS AT ZERO INTEREST.
STOCK UP ON CAT PARTS TODAY!
Pay over the next 3 years at 0 interest with a Cat Card account.
Cat Rubber Tracks
STOCK UP NOW ON RUBBER TRACKS AND
DON'T PAY TILL 2026
Until Sept 30, Peterson Cat is offering big discounts on Genuine Cat rubber tracks, with a special incentive when you buy online:
30% OFF Cat rubber tracks when you purchase from the parts counter
40% OFF when you buy online at parts.cat.com with promo code TRACKS40
Stock up today and save—this offer won't last forever!
PLUS, get 0% for 36 months with NO PAYMENTS for the first 6 months with your Cat Card.
Offer ends September 30, 2025. Offer valid on select Cat rubber tracks, subject to availability. Additional terms and restrictions may apply. Promotion discounts referenced are not stackable with any other discount programs.
**A $3,500 minimum purchase invoice is required for the 0% for 36 months terms unless otherwise stated. Rental transactions do not count toward $3,500 minimum. Offer applies to construction industry customers only. Offer does not apply to Purchases subject to invoice billing (see your Cat Card agreement for invoice billing terms). Financing is subject to credit approval by Caterpillar Financial Commercial Account Corporation. Not all customers will qualify. Special offers are subject to change without notice, and additional terms and conditions may apply. Visit Catcard.com or contact your Cat dealer for more information.
STOCK UP NOW ON RUBBER TRACKS AND
DON'T PAY TILL 2026
Until Sept 30, Peterson Cat is offering big discounts on Genuine Cat® rubber tracks, with a special incentive when you buy online:
30% OFF Cat rubber tracks when you purchase from the parts counter
40% OFF when you buy online at parts.cat.com with promo code TRACKS40
Offer ends September 30, 2025. Offer valid on select Cat rubber tracks, subject to availability. Additional terms and restrictions may apply. Promotion discounts referenced are not stackable with any other discount programs.
**A $3,500 minimum purchase invoice is required for the 0% for 36 months terms unless otherwise stated. Rental transactions do not count toward $3,500 minimum. Offer applies to construction industry customers only. Offer does not apply to Purchases subject to invoice billing (see your Cat Card agreement for invoice billing terms). Financing is subject to credit approval by Caterpillar Financial Commercial Account Corporation. Not all customers will qualify. Special offers are subject to change without notice, and additional terms and conditions may apply. Visit Catcard.com or contact your Cat dealer for more information.
Rubber Track Undercarriage
WORK PRODUCTIVELY. TREAD LIGHTLY.
Cat rubber tracks help any machine – Cat machine or other brand – go where steel tracks can't. With Cat rubber tracks, you can customize compact track loaders or mini excavators to your work and your terrain. Rigorously tested for fit and performance, they give your machines a softer touch on the ground while working as hard as you need them to on the job.
California Customers
California customers can purchase Cat rubber tracks useing this link to parts.cat.com.
OR/WA Customers
Oregon and Washington can purchase Cat rubber tracks useing this link to parts.cat.com.
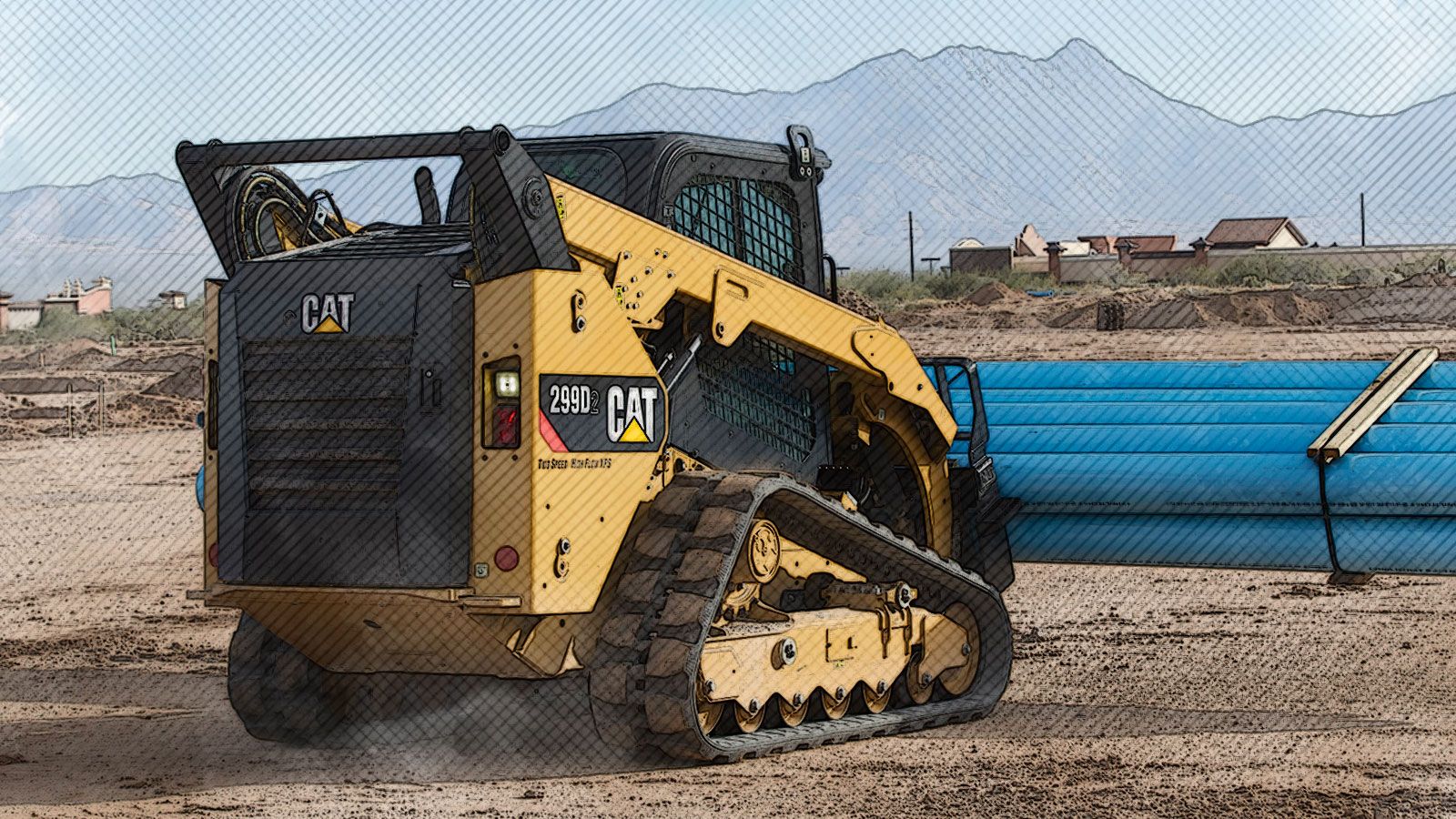
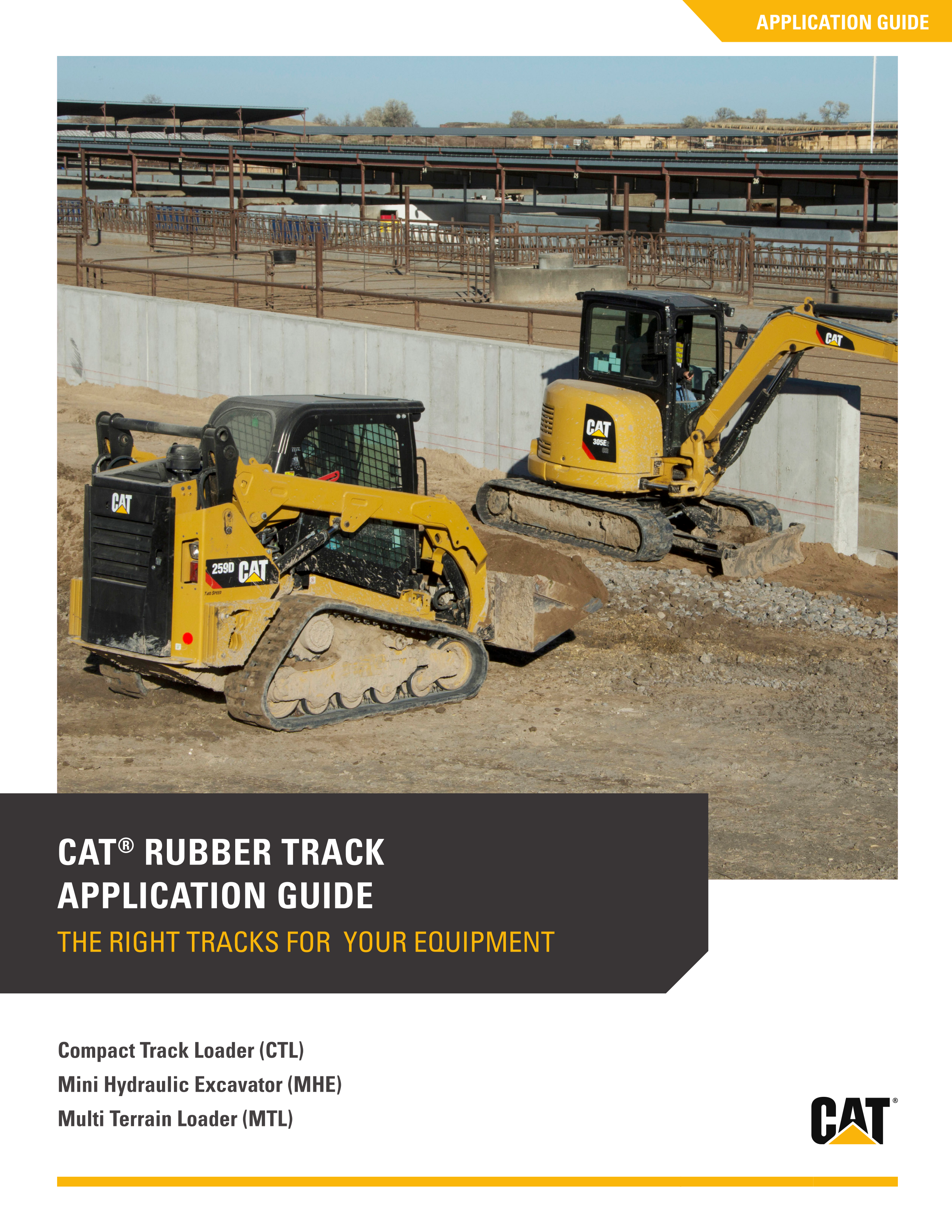
Designed Specifically To Drive Your Entire Fleet
Every rubber track is made to match the job. Some minimize ground disturbance; others are all about traction. Take a closer look at the rubber track designed for your equipment.
Cat Rubber Track Application Guide
The Right Tracks for you Your Equipment
Designed Specifically To Drive Your Entire Fleet
Every rubber track is made to match the job. Some minimize ground disturbance; others are all about traction. Take a closer look at the rubber track designed for your equipment.
Cat Rubber Track Application Guide
The Right Tracks for you Your Equipment
August is Wear Month
REPAIR TODAY!
30% OFF CAT WEAR PARTS AND UP TO 15% OFF LABOR*!
Don’t Pay until 2026 and 0% financing
Until September 30, Peterson Cat is offering HUGE discounts on some of the most popular Genuine Cat® Parts—with a special incentive when you buy online at parts.cat.com:
30% OFF all Cat GET (blades, tips, edges, etc)
30% OFF Cat General Duty and Heavy Duty Undercarriage
30% OFF all Cat Rubber Tracks
40% OFF all Rubber Tracks and GET when you purchase online at parts.cat.com with promo code TRACKS40 / GET40
*For a limited time, Peterson is offering discounts on labor when you bring your equipment to our shops. If your invoice total is greater than $5000, get 15% labor discount, less than $5000, get 10% discount. And when you finance parts and labor with a Cat Card, you’ll get 0% interest for 36 months with no payments until 2026!
Offer ends September 30, 2025. Discounts listed are not stackable with any existing discounts. Peterson Cat will honor whichever discount is greater. Additional terms and restrictions may apply. Offer subject to availability. Excludes Managed or Corporate Accounts. Talk to your Peterson Cat rep for more information.
Does not include machine rebuilds. Does not include existing repair work started before August 2025. Does not include field service or lube service. Does not apply to freight or transport. Cannot be combined with any other labor discounts.
**A $3,500 minimum purchase invoice is required for the 0% for 36 months terms unless otherwise stated. Rental transactions do not count toward $3,500 minimum. Offer applies to construction industry customers only. Offer does not apply to Purchases subject to invoice billing (see your Cat Card agreement for invoice billing terms). Financing is subject to credit approval by Caterpillar Financial Commercial Account Corporation. Not all customers will qualify. Special offers are subject to change without notice, and additional terms and conditions may apply. Visit Catcard.com or contact your Cat dealer for more information.
REPAIR TODAY
30% OFF CAT WEAR PARTS AND UP TO 15% OFF LABOR*!
Don’t Pay until 2026 and 0% financing
Until September 30, Peterson Cat is offering HUGE discounts on some of the most popular Genuine Cat® Parts—with a special incentive when you buy online at parts.cat.com:
30% OFF all Cat GET (blades, tips, edges, etc)
30% OFF Cat General Duty and Heavy Duty Undercarriage
30% OFF all Cat Rubber Tracks
40% OFF all Rubber Tracks and GET when you purchase online at parts.cat.com with promo code TRACKS40 / GET40
*For a limited time, Peterson is offering discounts on labor when you bring your equipment to our shops. If your invoice total is greater than $5000, get 15% labor discount, less than $5000, get 10% discount. And when you finance parts and labor with a Cat Card, you’ll get 0% interest for 36 months with no payments until 2026!
Offer ends September 30, 2025. Discounts listed are not stackable with any existing discounts. Peterson Cat will honor whichever discount is greater. Additional terms and restrictions may apply. Offer subject to availability. Excludes Managed or Corporate Accounts. Talk to your Peterson Cat rep for more information.
Does not include machine rebuilds. Does not include existing repair work started before August 2025. Does not include field service or lube service. Does not apply to freight or transport. Cannot be combined with any other labor discounts.
**A $3,500 minimum purchase invoice is required for the 0% for 36 months terms unless otherwise stated. Rental transactions do not count toward $3,500 minimum. Offer applies to construction industry customers only. Offer does not apply to Purchases subject to invoice billing (see your Cat Card agreement for invoice billing terms). Financing is subject to credit approval by Caterpillar Financial Commercial Account Corporation. Not all customers will qualify. Special offers are subject to change without notice, and additional terms and conditions may apply. Visit Catcard.com or contact your Cat dealer for more information.
Services Commitment
OUR SERVICES COMMITMENT MEANS YOUR PARTS & SERVICE NEEDS ARE OUR TOP PRIORITY
Parts when promised—or you get paid. As part of our Services Commitment in a CVA, your maintenance parts will be available by the next business day. Common repair parts? By the second business day. If they're not, we'll help cover costs by giving you a Cat Credit for the value of the late part, up to $1,000.
Parts Support CVA
Parts when promised – or we pay (Parts availability)
- Maintenance parts by the end of the next business day
- If maintenance parts aren't available by end of next business day or when you need them (promise date), we'll help cover the costs of your parts up to $1,000 in Cat Credits
Premium Service CVA
Parts when promised – or we pay (Parts availability)
- Maintenance parts by the end of the next business day
- Common repair parts by the end of the second business day
- If maintenance parts (end of next business day) or common repair parts (end of the 2nd business day) aren't available when you need them (promise date), we'll help cover the costs of your parts up to $1,000 in Cat Credits
Services Priority – or we pay (Technician availability)
- Priority appointment scheduling, diagnostics and progress updates
- Second-day technician response time to address unplanned repairs
- If response time exceeds two business days, we’ll help cover the costs of labor up to $1,000 of Cat Credits
Parts guarantees are associated with specific machine serial numbers; to qualify for delivery guarantee, a part must be intended for use in a machine covered by a qualifying CVA.